Introduction
Everyone produces urine daily from before they are born to the day they die. You don’t usually give much thought to it, unless you need to collect a urine sample or have just eaten asparagus. Since the development of centralized sewage treatment plants, we have been distanced from our own waste product and most people would consider it as no more than an inconvenience. However, in many cultures urine has religious, cultural and historical significance.1,2 For example, people consume eggs boiled in young boys’ urine during spring in a small town in China. The locals believe it has health benefits, but none have been proven. One person’s urine may well be another's treasure. This article will take you through a few of the commonly used substances discovered from urine and give you an overview on how urine may help to solve global crises.
Substances arising from urine
The most well-known substance isolated from urine is elemental phosphorus, which is credited to 17th century German alchemist Hennig Brand.3,4 Because of the similar colour, he believed that urine contained gold. After concentrating 5000 L of urine that he collected from a pub, removing salt and heating strongly for 16 hours, he discovered a substance that glowed in the dark, which he named phosphorus meaning “light bearer”. The chemical basis of Brand’s experiment can now be understood that he thermally decomposed the phosphate isolated from urine to liberate phosphorus. The glow was the result of the highly reactive phosphorus burning in the presence of oxygen.
Although he did not isolate gold from urine, his discovery of phosphorus led to the invention of matches in 1830.5 Despite that each of the early matches contained enough highly toxic white phosphorus to kill an adult, people embraced this invention with enthusiasm. Since then, phosphorus has become an essential resource for modern society and global demand has increased steadily.6 The greatest demand comes from agricultural use and food production. Thermal decomposition of phosphate is still the major process to obtain phosphorus, but from mineral sources.7 However, non-renewable mineral phosphate deposits with acceptable heavy metal levels are expected to be depleted in the near future. Thus, increased attention has turned towards recovery from both human and animal excretions.4,8,9
The most abundant substance in freshly produced urine is urea, but it is quickly converted into ammonia/ammonium by the action of urease, which is one of the fastest acting known enzymes .10,11 The release of ammonia gas gives urine its characteristic unpleasant smell and is responsible of nitrogen loss from urine. Ammonia and ammonium compounds are amongst the earliest substances that human learnt to utilise and manipulate. They have been known in many ancient cultures, including Roman, Greek, Persian and Chinese12–14. Ammonia is named after the Greek god “Ammon”, because sal ammoniac (salt of ammon) used to be collected by the temple of Ammon in ancient Greek and people once believed that “man and all life rose spontaneously from a sea of ammonia”.15 Interestingly, ammonia was described in Persian literature as “juice of lemon”.12 I fail to see the similarity between a decayed urine smell and a pleasant lemony aroma. In my opinion, the Greek “soaring eagle” and Chinese “brain salt” are better at describing the pungency and how it seems to penetrate your brain. Ammonia found many uses in ancient societies, such as cleaning, leather tanning and medicine. It is believed that Romans in the 1st century were already able to capture ammonia from decayed urine as struvite precipitate following intrinsic procedures, which usually involve distillation of urine and mixing the distillate with residue magnesium and phosphate (usually from plant sources) to produce struvite (Eq. 1).12,13 Solid struvite is much easier to transport and releases ammonia simply by heating.
NH4+ (aq) + Mg2+(aq) + PO43-(aq) → NH4MgPO4.6H2O (s) (Eq. 1)
Today, ammonia is the second largest chemical industry in the world (after sulfuric acid).16 Its global production reached 150 million tons in 2022 with a market value of USD $66.37 billion.17,18 86% of the ammonia is used as fertiliser or to produce fertiliser, while the remainder is used in a wide variety of industries, including explosives, cleaning products, batteries, refrigerant gas and in water treatment.19 The modern ammonia manufacturing industry primarily uses the Haber-Bosch process, with the first factory built in 1911.20 The process may appear simple (Eq. 2), but it is very energy and carbon intensive.16,21 Both the production of the starting material hydrogen gas and the Harber-Bosch reaction require high temperature and pressure, and hydrogen gas is largely produced from natural gas sourced methane.20,22,23 Ammonia production alone accounts for 1-2% CO2 equivalent of global greenhouse gas emissions.
N2 (g) + 3H2 (g) → 2NH3 (g) (Eq. 2)
Aside from ammonia, nitrogen in urine can also be used to produce nitrate, which is the readily available nitrogen source for plants.24 Naturally, atmospheric nitrogen and nitrogen-containing organic matter such as urea, are converted to ammonium and nitrate by some bacteria and fungi living within soil.25,26 Although this process was not well understood until 1877,27 nitrate has been an important substance since early civilisation, particularly potassium nitrate, commonly known as saltpetre. The earliest recorded use of saltpetre can be traced back to the Han dynasty in ancient China (202 BC – 9 AD, 25–220 AD) used in the glass making process.28
Along with other uses such as medicine and cooling wine,29 the use of saltpetre to make gunpowder had the most significant impact on history. By the Song dynasty (960-1279), saltpetre manufacturing was already regulated by the government to ensure continuous and exclusive supply to the Chinese army (Fig. 1).30 Early production of saltpetre relied on the gathering of aged agricultural soil that had been mixed with urine and manure from dry regions, and a small amount from mineral deposits.29 Most of the nitrate in soil exists as calcium nitrate, so conversion into potassium nitrate is needed, by treating with potassium carbonate from plant ash.
Because of the huge advantage of gunpowder over traditional weapons, ancient Chinese failed to keep this technology secret from the rest of world, which made potassium nitrate a resource in high demand.31 Amongst the search to increase potassium nitrate production, there was a patented process of making potassium nitrate from urine in 1626, which utilises the natural process by fermenting urine in soil for a minimum of three months.32 Despite the promise of producing 1000 tons of saltpetre every six months if every household in England fermented their urine, this scheme never gained popularity with the public.
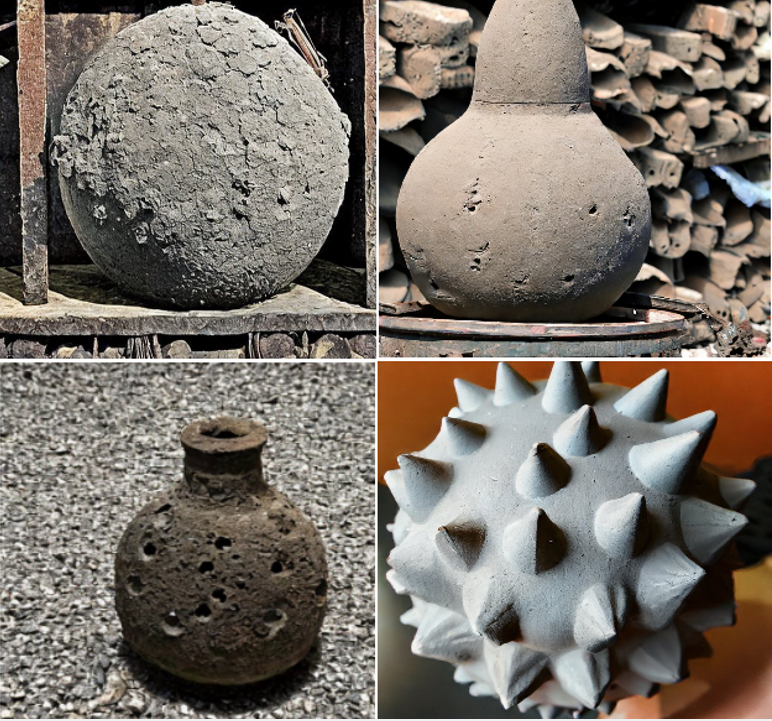
Although nitrate’s importance in warfare has diminished in modern societies, it is still an essential chemical ingredient in a wide range of industries, especially in fertilisers.33–36 The common nitrates used as fertilisers including ammonium, sodium, potassium and calcium salts, are commonly produced from ammonia via the Oswald process.37 In addition to the unsustainable and energy intensive production process, increasing study has concentrated on nitrates’ adverse environmental and health effects resulting from overuse, including eutrophication, blue baby syndrome and various cancers.38–40 Since 1998, the World Health Organization has recommended that nitrate levels in drinking water should not exceed 50 mg/L (or 11.3 mg/L as N)41,42 and New Zealand drinking water standards followed the same recommendation.43 However, nitrate contamination remains a major threat to public health because most of the exposure occurs from unregulated private water supplies, and some evidence shows that the current standard may still be too high.44,45
Global crises and new developments
Despite the problems with phosphorus, ammonia and nitrates, their global demand for food production has continued to rise under pressure. The current manufacturing practices are worsening the food, energy and environmental crises society is facing. Many scientists believe that urine may hold a key to solve some of these problems. The solution could kill two birds with one stone: making use of the rich macronutrients and micronutrients in urine as fertilisers or to feed into chemical industries, whilst also reducing environmental damage and health risks caused by sewage discharge. Although a quick web search would give you lots of gardening tips on how to make fertiliser from your own urine, doing it on scale and as part of society’s waste management system isn’t so straight forward. Even an operation as small as my father’s one-pot home fermentation was problematic as the urine operation received continuous malodour complaints and never gained approval from other household members. A centralised urine treatment system would have many more aspects to consider.
Most industrialised countries use centralised sewage treatment, which has helped to improve public health and hygiene. However, this collection system is not ideal for nutrient recovery, because urine is significantly diluted by other less nutrient-rich household wastewater. Despite representing only 1% in wastewater volume, urine contributes 75-85% of the nitrogen and 50% of the phosphorus in domestic wastewater.46 This dilution both increases the complexity of the mixture and makes the recovery of nutrients more difficult and less efficient. However, there has been some success with the recovery of single nutrients, either nitrogen or phosphorus from wastewater plants.47–49 The most successful phosphorus recovery strategies are based on a modernised version of the ancient struvite precipitation technology. This method can produce high quality struvite that can be directly applied in agriculture.50,51 Struvite as a fertiliser can supply nitrogen, phosphorus and magnesium to the soil, and because of its low solubility in water, it is slow release and therefore less likely to be washed away and contaminate the surrounding environment.52Struvite formation can also recover ammonium, but because of the nitrogen and phosphorus imbalance, additional phosphorus is needed to aid full nitrogen recovery.
Nitrogen in wastewater is viewed as a problem. Most modern wastewater treatment plants include steps to remove nitrogen before discharging, usually by biological process involving nitrification and denitrification.53 However, the increased demand for nitrogen resources has promoted a shift towards nitrogen recovery rather than removal.46 This has been an active field, with a lot of new development. One notable technology that has been gaining interest in wastewater treatment is bio-electrochemical systems, which have the potential to generate electricity or hydrogen alongside nutrient recovery. Although bioelectricity has been known since the 18th century,54 it wasn’t until 1911 that the first microbial fuel cell was reported, which enabled the harvesting of electricity from biological decomposition of organic matter.55 More recently, sound efficiency using these systems to recover nitrogen from wastewater has been shown ,46,56 but to develop a commercial system that can also provide a reliable energy source, there are still challenges to overcome, such as low stability, low voltage and high cost.57
Another approach to energy and resource recovery from wastewater is to produce algal biomass, which can be used to produce either fertiliser, biofuel or bioplastic.58 An added advantage of this approach is that algal growth consumes large quantities of carbon dioxide; on average, 1 kg of algae consumes 1.8 kg of carbon dioxide every day, offering a potential solution to removing excess greenhouse gas from the atmosphere. Algal biomass production is a mature industry, which has been supplying the food, nutritional supplement and animal feed industries. However, its requirements for land, water and nutrient input are high, thus making production expensive. Having the production as part of the wastewater treatment plant reduces water and nutrient requirements, thus reducing cost, potentially becoming price competitive with fossil fuels.58–61
Nutrient recovery from urine often requires less processing and is more efficient than recovery from wastewater, with lower risk of heavy metal residues and pathogen contamination.11 However, the high water content and low value of urine mean that transportation costs could hinder centralised processing. To overcome this problem, many studies suggest a source recovery approach, where urine is separated, collected and treated onsite as it is produced. This can simplify the recovery process while reducing emissions and transportation cost.62 The biggest challenge for this approach is that toilet and sewage systems would require redesign and expensive reinstallation.63 There has been considerable effort focussed on dry urine-diverting toilets to aid nutrient recovery, reduce environmental impact and improve sanitation for low income countries.10,64,65 The energy and nutrient recovery methods for wastewater previously discussed can also be applied to urine.46 The major composition of urine is similar to that of synthetic fertilisers; thus urine can be converted to liquid fertiliser with minimal processing. This approach has enabled the world’s first approved fertiliser originating from urine for edible vegetables - Aurin.63 Because of the nutrient richness of urine, 100 L of the fertiliser can be made from 1,000 L of urine through nitrification, filtration and distillation.
Apart from the technical challenges, social acceptance for using urine-derived products must also be obtained. Research has shown that the acceptance of urine diverting dry toilet is high, but the acceptance level of using urine-derived fertiliser varied widely between different regions.66–68 In the areas with low acceptance of urine, the major challenges are views of religious impurity, perception of low agricultural value and handling difficulties.66 Interestingly, acceptance of using faecal matter in agriculture has higher acceptance than urine in some cultures, with the use of faecal matter in agriculture already a common practice, with relatively mature techniques and the fertiliser value is more recognised. However, most of the nutrients important for crop growth are excreted in urine. In low socioeconomic areas, introduction of urine-based fertiliser will not only improve nutrient recovery, but also help to improve access to resources.
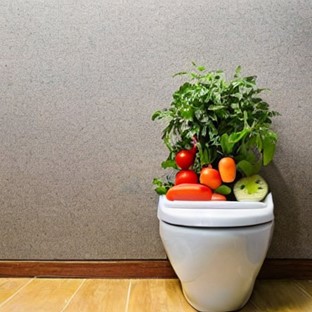
Conclusions
Urine has led to remarkable developments throughout history, including the discovery of phosphorus, ammonia and nitrate, which are now important manufactured chemicals. There are promising indications that urine may once again be one solution to the current environmental, food and energy challenges society is facing. There are still many hurdles before establishing modern systems to recover sufficient nutrients and energy from urine to make a significant impact in replacing the use of fossil fuels. This article briefly discussed some of the recent developments and challenges regarding resource recovery from urine and wastewater. These methods and technologies such as struvite precipitation, algal biomass production, bio-electrochemical systems and urine diverting dry toilet offer great potential for improvement on current practices, leading to a greener and more sustainable future.
References
- Cowan, D. F. Can. J. Comp. Med. Vet. Sci. 1960, 24, 216–221.
- Bourke, J. G. Compilation of Notes and Memoranda Bearing Upon the Use of Human Ordure and Human Urine in Rites of a Religious Or Semi-Religious Character Among Various Nations; Verlag nicht ermittelbar, 1888.
- Jamal, J., E. J. Urol. 2008, 179, 309.
- Krafft, F. Angew. Chem., Int. Ed. Engl. 1969, 8, 660–671.
- Gleason, W. JOM 2007, 59 (6), 17–19.
- Wang, Z.; Yin, Y.; Liu, G.; Lun, F.; Zhang, F.; Cui, Z.; Wu, J. Sci. Total Env. 2022, 830, 154484.
- Melville, J. F.; Licini, A. J.; Surendranath, Y. ACS Cent. Sci. 2023, 9, 373–380.
- Ashley, K.; Cordell, D.; Mavinic, D. A. Chemosphere 2011, 84, 737–746.
- Cordell, D.; White, S. Agronomy 2013, 3, 86–116.
- Kundu, S.; Pramanik, B. K.; Halder, P.; Patel, S.; Ramezani, M.; Khairul, M. A.; Marzbali, M. H.; Paz-Ferreiro, J.; Crosher, S.; Short, G.; Surapaneni, A.; Bergmann, D.; Shah, K. J. Env. Chem. Eng. 2022, 10, 107146-107170.
- Martin, T. M. P.; Esculier, F.; Levavasseur, F.; Houot, S. Crit. Rev. Env. Sci. Tech. 2022, 52, 890–936.
- Sutton, M. A.; Van Dijk, N.; Levy, P. E.; Jones, M. R.; Leith, I. D.; Sheppard, L. J.; Leeson, S.; Sim Tang, Y.; Stephens, A.; Braban, C. F.; Dragosits, U.; Howard, C. M.; Vieno, M.; Fowler, D.; Corbett, P.; Naikoo, M. I.; Munzi, S.; Ellis, C. J.; Chatterjee, S.; Steadman, C. E.; Móring, A.; Wolseley, P. A. Phil. Trans. R. Soc. A. 2020, 378, 20190315.
- Witty, M. Acta Archaeologica 2016, 87, 179–191.
- Multhauf, R. P. Technol. Culture 1965, 6, 569–586.
- Shawcross, D. L.; Damink, S. W. M. O.; Butterworth, R. F.; Jalan, R. Metab. Brain Dis. 2005, 20, 169–179.
- Giddey, S.; Badwal, S. P. S.; Munnings, C.; Dolan, M. ACS Sustain. Chem. Eng. 2017, 5, 10231–10239.
- ReportLinker. Ammonia Global Market Report 2022. GlobeNewswire News Room. https://www.globenewswire.com/news-release/2022/09/30/2526273/0/en/Ammonia-Global-Market-Report-2022.html (accessed 08/06/2023).
- Ammonia production worldwide 2022. Statista. https://www.statista.com/statistics/1266378/global-ammonia-production/ (accessed 08/06/2023).
- Maxwell, G. Synthetic Nitrogen Products: A Practical Guide to the Products and Processes; Springer Science & Business Media, 2006.
- Humphreys, J.; Lan, R.; Tao, S. Adv. Energy Sustain. Res. 2021, 2, 2000043.
- MacFarlane, D. R.; Cherepanov, P. V.; Choi, J.; Suryanto, B. H. R.; Hodgetts, R. Y.; Bakker, J. M.; Ferrero Vallana, F. M.; Simonov, A. N. Joule 2020, 4, 1186–1205.
- Smith, C.; K. Hill, A.; Torrente-Murciano, L. Energy Env. Sci. 2020, 13, 331–344.
- Ghavam, S.; Vahdati, M.; Wilson, I. A. G.; Styring, P. Front. Energy Res. 2021, 9.
- Dechorgnat, J.; Nguyen, C. T.; Armengaud, P.; Jossier, M.; Diatloff, E.; Filleur, S.; Daniel-Vedele, F. J. Exp.Botany 2011, 62, 1349–1359.
- Stein, L. Y.; Klotz, M. G. Current Biol. 2016, 26, R94–R98.
- Stevenson, F. J. In Agronomy Monographs (Ed.: Stevenson, F. J.), American Society of Agronomy, Crop Science Society of America, Soil Science Society of America, Madison, WI, USA, 2015, 1–42.
- Sedlacek, C. J. Front. Microbiol. 2020, 11, 1900.
- Gan, F.; Cheng, H.; Li, Q. Sci. China Ser. E. 2006, 49, 701–713.
- Barnum, D. W. J. Chem. Educ. 2003, 80, 1393.
- Lorge, P. In Science and Confucian Statecraft in East Asia, Brill, 2019, 31–44.
- Ponting, C. Gunpowder: An Explosive History - from the Alchemists of China to the Battlefields of Europe, Random House, 2011.
- Cressy, D. Saltpetre: The Mother of Gunpowder, OUP: Oxford, 2013.
- Joshi, C. S.; Shukla, M. R.; Patel, K.; Joshi, J. S.; Sahu, O. Int. Lett. Chem. Phys. Astr. 2015, 41, 88-99.
- Honikel, K.-O. Meat Sci. 2008, 78, 68–76.
- Martini, E. C.; Favoreto, M. W.; Rezende, M.; de Geus, J. L.; Loguercio, A. D.; Reis, A. Clin. Oral Invest. 2021, 25, 4311–4327.
- Butler, A. R.; Feelisch, M. Circulation 2008, 117, 2151–2159.
- Bajpai, S.; Alam, N.; Biswas, P. In Separation Science and Technology Vol. 11. (Ed.: Ahuja, S.), Academic Press, 2019, 85–112.
- Ward, M. H. Rev. Environ. Health 2009, 24, 357–363.
- Reddy, V. R.; Cunha, D. G. F.; Kurian, M. Water 2018, 10, 101.
- Smolders, A. J. P.; Lucassen, E. C. H. E. T.; Bobbink, R.; Roelofs, J. G. M.; Lamers, L. P. M. Biogeochem. 2010, 98, 1–7.
- World Health Organization; Safety I. P. on C. Guidelines for drinking-water quality. Vol. 2, World Health Organization, 1996.
- Guidelines for Drinking-Water Quality, 4th Edition, Incorporating the 1st Addendum. https://www.who.int/publications-detail-redirect/9789241549950 (accessed 19/06/2023).
- Water Services (Drinking Water Standards for New Zealand) Regulations 2022; 2022, 7. https://www.legislation.govt.nz/regulation/public/2022/0168/latest/whole.html (accessed 19/06/2023).
- Grout, L.; Chambers, T.; Hales, S.; Prickett, M.; Baker, M. G.; Wilson, N. Environ. Health 2023, 22, 9.
- Chambers, T.; Douwes, J.; Mannetje, A.; Woodward, A.; Baker, M.; Wilson, N.; Hales, S. Aust. NZ J. Pub. Health 2022, 46, 105–108.
- Beckinghausen, A.; Odlare, M.; Thorin, E.; Schwede, S. Appl. Energy 2020, 263, 114616.
- Ye, Y.; Ngo, H. H.; Guo, W.; Liu, Y.; Chang, S. W.; Nguyen, D. D.; Liang, H.; Wang, J. Bioresource Tech. 2018, 268, 749–758.
- de-Bashan, L. E.; Bashan, Y. Water Res. 2004, 38, 4222–4246.
- Sena, M.; Seib, M.; Noguera, D. R.; Hicks, A. J. Cleaner Prod. 2021, 280, 124222-124234.
- Cieślik, B.; Konieczka, P. J. Cleaner Prod. 2017, 142, 1728–1740.
- Ma, P.; Rosen, C. Chemosphere 2021, 274, 129609-129626.
- Kataki, S.; West, H.; Clarke, M.; Baruah, D. C. Conservation Recycl. 2016, 107, 142–156.
- McCarty, P. L. Environ. Sci. Technol. 2018, 52, 3835–3841.
- Flimban, S. G. A.; Ismail, I. M. I.; Kim, T.; Oh, S.-E. Energies 2019, 12, 3390-3410.
- Potter, M. C.; Waller, A. D. Proc. Royal Soc. Lond. B 1997, 84, 260–276.
- Cerrillo, M.; Riau, V.; Bonmatí, A. Membranes 2023, 13, 186-208.
- Mahmoud, R. H.; Gomaa, O. M.; Hassan, R. Y. A. RSC Adv. 2022, 12, 5749–5764.
- Park, J. B. K.; Craggs, R. J.; Shilton, A. N. Bioresource Technol. 2011, 102, 35–42.
- Arora, K.; Kaur, P.; Kumar, P.; Singh, A.; Patel, S. K. S.; Li, X.; Yang, Y.-H.; Bhatia, S. K.; Kulshrestha, S. Front. Energy Res. 2021, 9.
- Ali, S. S.; Mastropetros, S. G.; Schagerl, M.; Sakarika, M.; Elsamahy, T.; El-Sheekh, M.; Sun, J.; Kornaros, M. Energy Rep. 2022, 8, 13253–13280.
- Mohsenpour, S. F.; Hennige, S.; Willoughby, N.; Adeloye, A.; Gutierrez, T. Sci. Total Env. 2021, 752, 142168-142191.
- Liu, Y.; He, L.-F.; Deng, Y.-Y.; Zhang, Q.; Jiang, G.-M.; Liu, H. Chem. Eng. J. 2022, 442, 136200-136215.
- Wald, C. Nature 2022, 602, 202–206.
- Liu, Y.; Zhang, Q.; He, L.-F.; Ran, Y.; Deng, Y.-Y.; Liu, H. Res. Conserv. Recycl. 2023, 190, 106807-106817.
- Conroy, K. M.; Mancl, K. M. Journal of Water, Sanit. Hygiene Dev. 2022, 12, 905–920.
- Harada, H. In The Sanitation Triangle: Socio-Culture, Health and Materials (Ed.: Yamauchi, T., Nakao, S., Harada, H.), Springer Nature, Singapore, 2022, 209–226.
- Lienert, J.; Larsen, T. A. Environ. Sci. Technol. 2010, 44, 556–566.
- Segrè Cohen, A.; Love, N. G.; Nace, K. K.; Árvai, J. Environ. Sci. Technol. 2020, 54, 5297–5305.