Abstract
Microplastics are ubiquitous in the atmosphere and have wide impacts across human health and climate change. The study of airborne microplastics is a relatively new field, which is hindered by sampling and analysis methods not being standardised. This review provides an overview of the various sampling and analysis methods for airborne microplastics. Greater understanding of sampler designs and resuspension is required. Sample preparation processes must be developed to remove organic debris while not affecting polymer types of interest. Analysis methods should be verified with blanks and controls and multiple analysis techniques should be utilised. It is important to highlight that different analysis methods are associated with varying levels of confidence in microplastic identification.
Introduction
The first synthesis of a synthetic polymer occurred in 1907 and since then the physical properties of plastics - including durability and light weight - combined with its economical production has led to significant increases in production and use.1,2 In 2019, the global annual plastic production was over 368 million metric tonnes and estimates suggested that plastic production would double in the next 20 years.3,4
Microplastics (MPs) and nanoplastics (NPs) are a class of environmental pollutants and are present in remote locations in the northern and southern hemisphere.5-7 Definitions vary but MPs are commonly defined as being between 1 to 5000 μm in size and can be produced by primary or secondary sources.8 Primary MPs are deliberately manufactured for use in areas like cosmetics,9 while secondary MPs are produced as a result of environmental degradation of larger plastics.10 NPs are another class of small plastics and are defined as being between 1 nm to 1 μm in size.9
Once released into the environment, mechanisms of environmental degradation of plastics include via ultraviolet radiation, seawater, microbes and macrofauna.11,12 Microplastics have various methods of dispersal, including winds, ocean currents and river flow and organisms.13 In particular, atmospheric transport allows for long-range transportation of MPs before dry (gravitational sedimentation) and wet (precipitation) deposition into terrestrial and aquatic environments.14
Plastic additives, which alter the physical and chemical qualities of plastics, are added during the manufacturing process and pose significant health risks.15 Brominated flame retardants are one such additive and have been identified as endocrine disruptors.15 It is not just through deliberate addition of chemicals that plastics can act as a vector for chemicals. Other environmental contaminants such as polychlorinated biphenyls and bisphenol A can sorb to MPs, leading to increases in concentration of up to one million times.16,17 Airborne MPs can damage the respiratory system at high concentrations, with those who are occupationally exposed at greater risk.18 The presence of MPs and NPs in the carotid artery plaque has been correlated with a greater risk of heart attacks, stroke and death in patients.19 Recent studies have found evidence of MPs in the human prostate, testes and semen; however, these studies do not determine the source of these MPs, are limited by small sample sizes and do not establish any links to toxicity.20,21 Additionally, MPs and NPs may contribute to climate change by interacting with light22 and clouds.23,24
Microplastics have long been understood to be a marine pollutant; however, it is only in the last decade that airborne MPs have been identified.25 Given the interest in the effects of MPs and NPs on human health and the climate, it is necessary to understand their distributions in space and time and the overall state of research in the field. Any meaningful understanding of airborne MPs and NPs requires comparisons between studies performed at different locations and times, which requires standardised sampling techniques and analysis. However, fast developments in the field have resulted in non-standardised methods meaning studies cannot be easily compared.26 This review will focus only on airborne MPs due to the large differences in sampling and analysis techniques relating to NPs.
Sample collection methods
The two most common sampler types for collecting airborne microplastics are deposition samplers and active samplers. Most studies use deposition samplers which collect atmospheric fallout and fewer studies use active samplers which pump air through a filter at a known flow rate.13, 27-29 Deposition samplers collect particles which settle due to wet and dry deposition while active samplers measure the concentration of MPs in the air by drawing air through a filter (Fig. 1).26 These different sampler types also produce different values and units, with deposition samplers providing calculated deposition rates in MPs/m2/day and active samplers providing concentrations of MPs in MPs/m3 which are not easily comparable.26 Measurements made using deposition or active sampling can be used to determine temporal and spatial patterns of deposition of MPs.
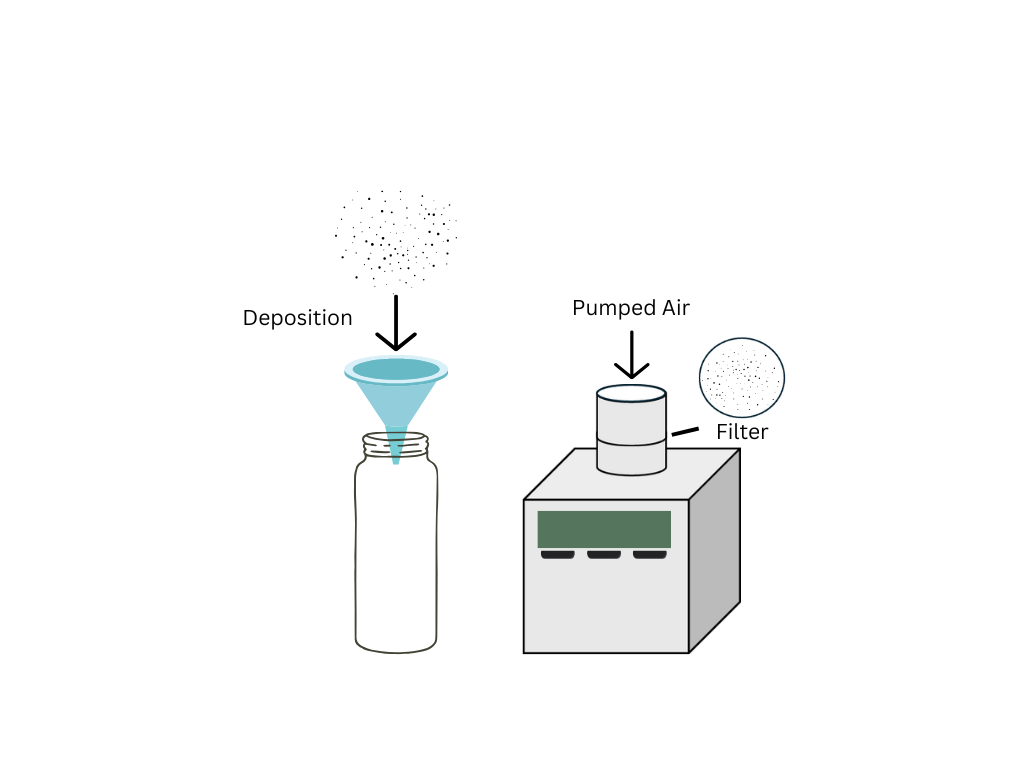
Bulk deposition involves the collection of both dry and wet deposition.14 Most studies use samplers composed of glass and metallic components and avoid plastic materials to prevent contamination. However, bulk deposition cannot be compared easily as equipment of different heights, areas, and periods of operation are used.26 Automatic wet and dry deposition samplers allow for the separation of wet and dry deposition fluxes but require more sophisticated samplers and power to collect samples in the presence or absence of precipitation. These samplers can be used to calculate depositions associated with particular events like wet deposition associated with monsoons.30 This could be of particular interest when investigating wet deposition which is believed to scavenge MPs from the air.31 Wet deposition of MPs has been correlated with urban sources, population centres and resuspension mechanisms, while dry deposition is positively correlated to higher wind speed and humidity.14,32
Resuspension of deposited MPs is a potential limitation when performing deposition sampling. Different sampler designs and sampling periods have been compared, suggesting that resuspension has some influence on the calculated deposition rates of microplastics.33,34 However, bulk deposition samplers are easy to use, cheap and do not require power contributing to their continued use despite uncertainties about resuspension. Deposition sampling is suitable for more sites, particularly remote locations where power is not readily available.
Active samplers are traditionally used to sample for total suspended particulates, PM10 and PM2.5 contamination (particulate matter of aerodynamic diameter < 10 µm and < 2.5 µm) of which MPs are a subset.35 This means that the samplers and protocols are much more standardised as compared to deposition sampling; however, they require greater knowledge to operate. This sampling method requires power to draw air through a filter with known pore sizes at a known flow rate. The intake flow rate can be adjusted as required and can be used to estimate the number of MPs inhaled by humans.36
Sample preparation
For sample preparation, there are several options and considerations depending on the collection type used. Sometimes no preparation step is completed and the direct filtration of sample material or the direct analysis of filters can be undertaken.37 However, it is common for a preparation method to be completed to limit the amount of organic material present in a sample and reduce interference in some analysis techniques.38 This can involve a density separation step and/or a digestion which is used to remove heavy inorganic contaminants while matrix digestion is used to remove organic debris.39
Methods of density separation and direct filtration retain organic debris which can affect identification and analysis, so often a combination of density separation and digestion is used.26,40,41 In cases where density separation is used to isolate MPs, solutions of density between 1.6-1.8 g/mL are optimal for separation.42 There are a range of digestion processes including the use of oxidisers, acids, alkalis, and enzymes.25,43 However, there is evidence to suggest that different digestion protocols affect the chemical and physical properties of the sampled MPs.44 Strong acid and base treatments are destructive to many common plastic types when tested on thin films, and oxidative treatment using hydrogen peroxide can degrade polyamide.45 Fenton’s reagent (hydrogen peroxide with an iron catalyst) has been shown to be effective; however, it can affect the results of analysis techniques like Raman spectroscopy and Nile Red fluorescence microscopy.46,47 Overall, there is no standardised method for separation and digestion and often the selection of sample preparation is determined by the desired sample analysis method which limits inter-laboratory comparison.46
Sample analysis and identification
There are many sample analysis methods, ranging from visual, spectroscopic and chemical determination of mass, which provide different information about microplastics including size distributions, polymer type and particle counts. These sample analysis methods have varying sensitivities and error rates which makes comparison between methods difficult. An important consideration for all analysis methods is the level of confidence in classifying particles as microplastics.
Criteria for confidence levels when identifying PFAS using mass spectrometric methods have been proposed and could be adapted for microplastics work.48 Weathering of MPs and sample digestion can lead to changes in the morphology of the plastics and affect most analysis methods.31 For example, MPs lose colour on the edge and surface and have irregular shapes with sharper edges and rougher surfaces because of weathering affecting visual identification methods.26,49,50 Weathering can also cause micro-scratches and changes to the surface polarity affecting Raman and FTIR spectra.51,52 A summary of the capabilities of the analysis methods is presented in Table 1.
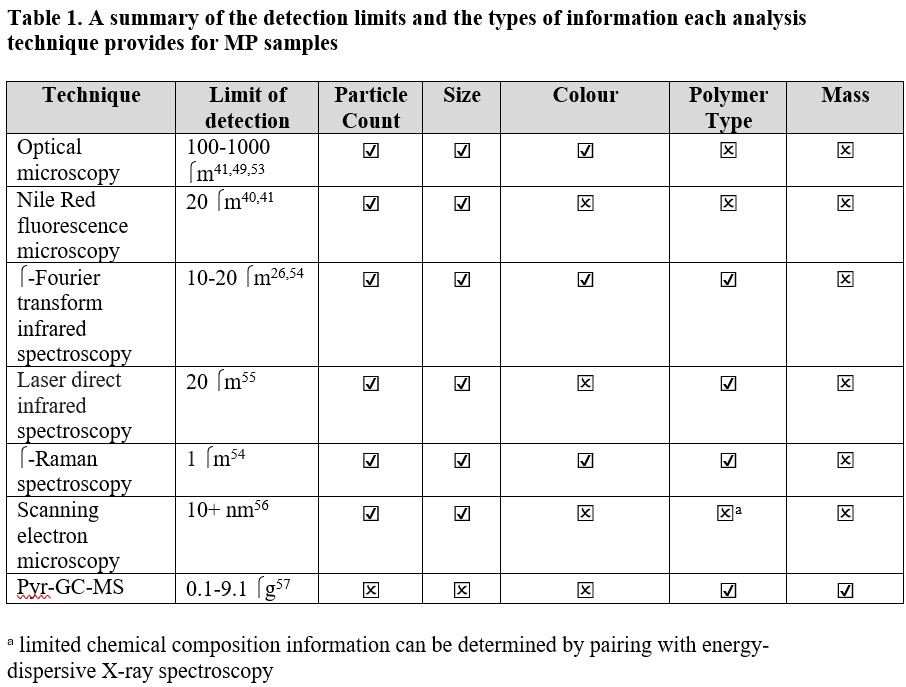
Optical microscopy
Visual inspection with a stereomicroscope allows for the determination of shape, colour, and size of larger MPs, with the limit of detection commonly stated as > 500 μm.9,58 This method of identification is severely limited by human error with different results based on the researcher performing the inspection. To limit the misidentification of MPs using visual inspection, a set of criteria is applied which looks at the presence of organic structure, consistent thickness and colour.25 Additionally, the hot needle test has been applied to aid in the determination of MPs. The procedure for the hot needle test is not standardised; however, a positive result for MPs should display a melting, softening or bending while a negative result will have no response or a slight movement with no shape change.59 Visual identification is significantly affected by human bias and size limitation due to low resolution.60 This technique can lead to error rates of up to 70% for identifying MPs, with increasing error rates as particle size decreases.50 The presence of organic and inorganic structures could further increase these errors.50
Nile Red fluorescence microscopy
Nile Red is a hydrophobic fluorophore which binds to neutral lipids and fluoresces strongly in a hydrophobic environment.61 Nile Red molecules can be absorbed by MPs and bind to their surfaces through van der Waals interactions and dipole interactions in the case of polar polymers.62 This results in fluorescence of particles that have sorbed Nile Red dye upon photoexcitation which can be observed using fluorescence microscopy (Fig. 2).
There are many different application methods of the solution of Nile Red, including adding drops of Nile Red solution post-filtration onto the filter,63 injection directly into samples prior to filtration before64 and after digestion,65 and transferring particles onto microscope slides and staining.66
A range of solvents have been used to dissolve the Nile Red dye including acetone, methanol, hexane, chloroform, ethanol and isopropyl alcohol.41 Dissolving the dye in acetone is most common; however, some papers select methanol as the solvent citing the resistance of common polymer types.40,41 The solvents are selected based on their ability to not damage the filters or MPs, as well as maintain a high recovery rate.
The fluorescence of Nile Red is influenced by its concentration, with 0.1-2 μg /mL having optimal fluorescence and greater concentrations lead to quenching.40 However, other studies have selected 10 μg/mL as an ideal concentration, balancing visibility of fluorescence and minimising background noise against the quenching that occurs at greater concentration.67 Fluorescence of common polymers has been investigated at multiple wavelengths, with excitation and emission wavelengths of 460 and 525 nm respectively having less contaminant fluorescence after digestion with hydrogen peroxide.40 Currently, Nile Red results should be verified alongside other polymer specific methods or compared to MP spiked samples to determine the precision of the filtration/separation and the effectiveness of the Nile Red.68,69
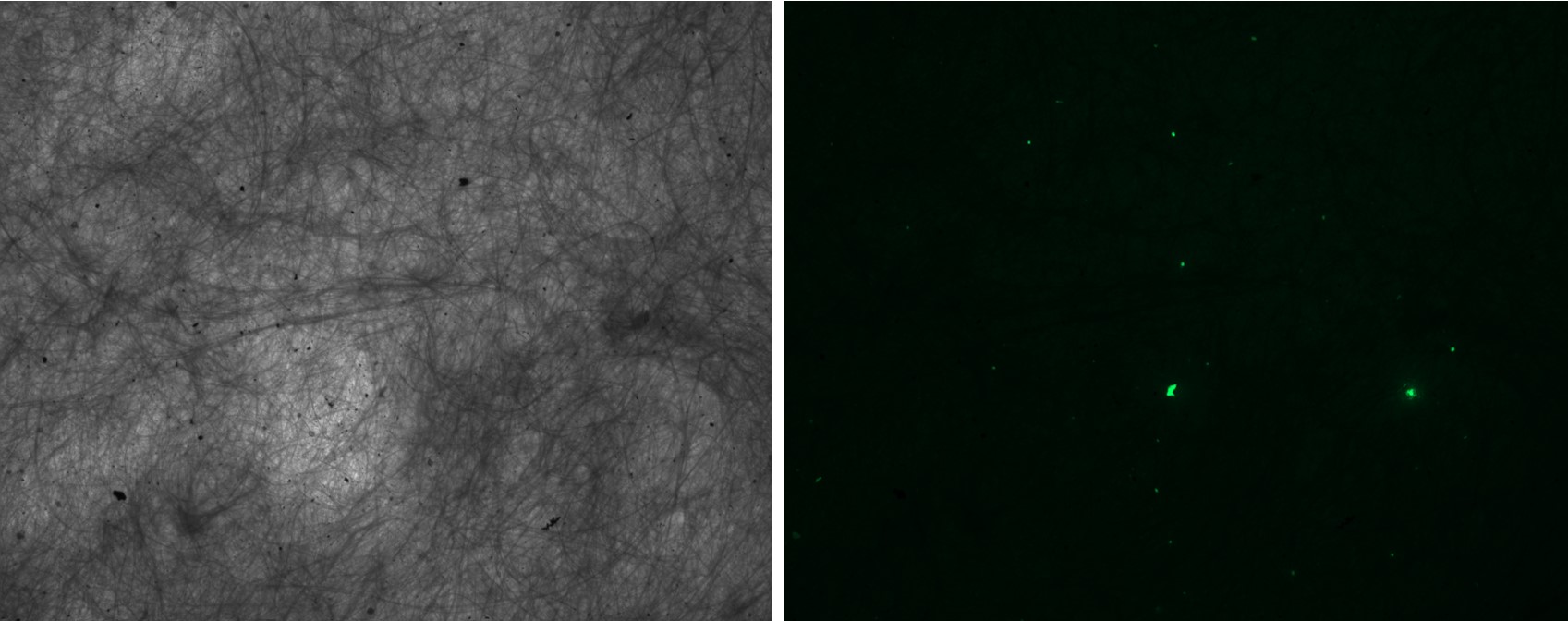
Fourier transform infrared spectroscopy and laser direct infrared spectroscopy
Fourier transform infrared spectroscopy (FTIR) involves the collection of vibrational spectra of MPs in the range of 400-4000 cm-1, which can then be matched to existing spectra in a reference library (Fig. 3).26 μ-FTIR spectroscopy methods utilise a microscope which allows for the detection of particles towards the limit of 10 μm in diameter.70 The added use of focal plane arrays (FPA) allows for a more streamlined workflow and allows analysis to a smaller size range. The use of IR compatible filters like alumina membrane filters also allow for a more timely process, eliminating the need to manually move particles onto a compatible substrate but these are costly.71 This technique has been shown to underestimate particle counts of particles below 20 μm by 35% compared to µ-Raman spectroscopy.70 FTIR has previously been used for quality control in the polymer industry meaning the existing spectral libraries of virgin polymer types are broad, although weathered plastic spectra are less available meaning environmental samples can be harder to accurately identify.72
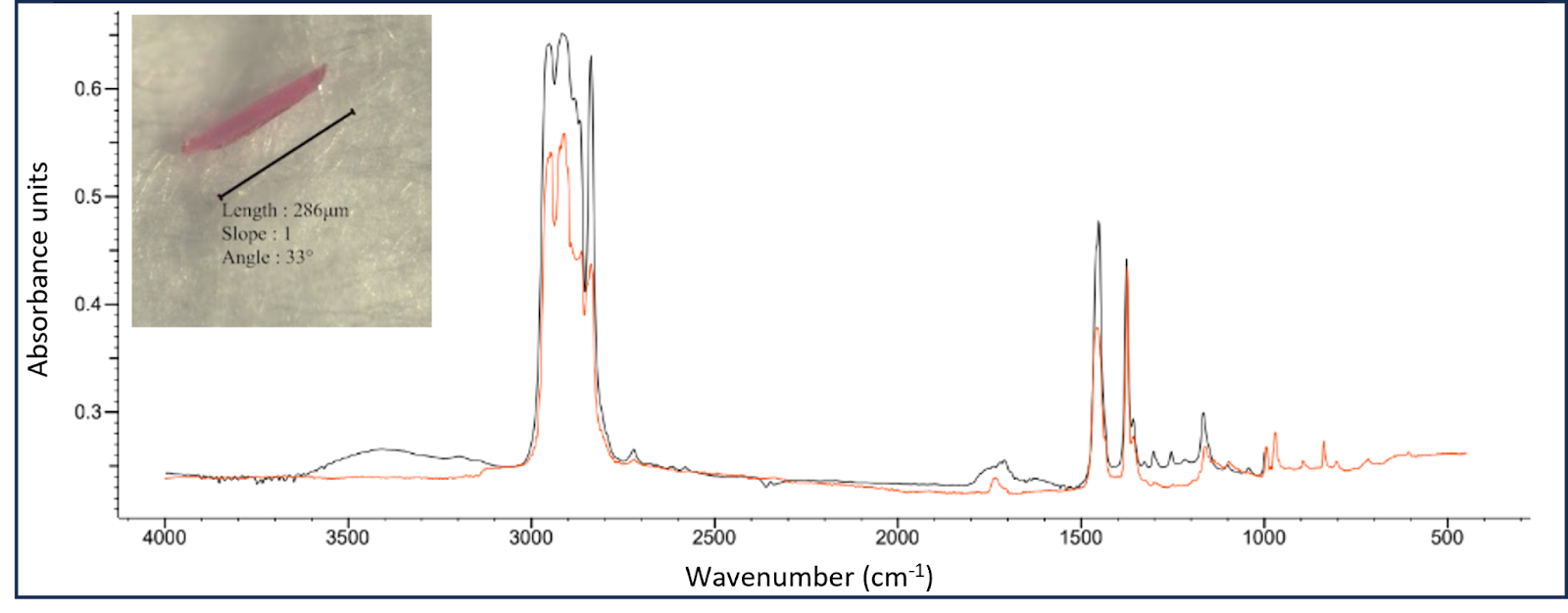
Laser direct infrared spectroscopy (LDIR) is similar to FTIR spectroscopy but uses a tuneable quantum cascade laser as the IR light source. This technique is able to produce stronger signals at faster rates when compared to the FPA FTIR system and does not require liquid nitrogen.73 The ability to automate LDIR increases throughput and reduces subjectivity of particle identification.55 However, the use of automated LDIR has had mixed results, producing incorrect matches in one study.27,74 Therefore, studies utilising LDIR should verify data to avoid errors in particle count, size measurements and false positives. Current manufacturer recommended methods are expensive and time intensive, requiring an initial particle sorting step followed by deposition of MPs in ethanol on a highly reflective glass slide.75
Raman spectroscopy
Raman spectroscopy excites the surface of a material with a high frequency laser resulting in photon emission. These emitted photons can be emitted parallel to the laser (Rayleigh scattering) or perpendicular to the laser (Raman scattering). Raman spectroscopy is newer to MP research than FTIR, so the spectra libraries are less developed.26 A μ-Raman spectrometer involves the use of a microscope alongside spectroscopy and has a spatial resolution of 1 μm and spectral resolution of 1 cm-1.51 The theoretical limitations of Raman spectroscopy are sub-μm; however, current techniques and weathering of MPs mean the current detection limit is around 1 μm.26,54 Raman spectroscopy has an inherently weak signal as a very small number of photons actually result in Raman scattering.76 Thus, a longer duration measurement is required, which increases the likelihood of laser-induced degradation of the sample MPs. Additionally, Raman spectroscopy has high fluorescence interference from organic contaminants, colouring agents, or the MPs themselves which can obscure the Raman signal.77 Raman spectrometers are expensive with estimated starting prices of USD 50,000 and can reach up to USD 400,000 for a spectrometer and equipment capable of performing automated analysis.78
Scanning electron microscopy and transmission electron microscopy
Scanning electron microscopy (SEM) and transmission electron microscopy (TEM) use high-energy electron beams to obtain images in greater resolution than is possible with light microscopy due to the limit of diffraction.79 SEM detects reflected electrons while TEM detects electrons that pass through the particle resulting in surface and internal information respectively.80 Energy-dispersive X-ray spectroscopy (SEM-EDS) can be used alongside SEM to provide chemical information.81 SEM-EDS detects X-rays emitted from interaction with the electron beam and generates a spectrum which can identify the elemental composition and be compared to existing literature.80 Some plastic particles such as PVC have unique characteristics like strong chlorine peaks in the EDS spectra, while other plastics including polypropylene and polyethylene have no distinctive EDS peaks.82
Pyrolysis coupled with gas chromatography-mass spectrometry
Pyrolysis coupled with gas chromatography-mass spectrometry (Pyr-GC/MS) measures the pyrolysis products of polymers meaning it is a very specific technique for select polymer types when calibrated and quantified properly.57,83 Samples are pyrolysed and the resulting pyrolysis products are chromatographically separated and detected using mass spectrometry. Pyr-GC/MS provides masses of collected microplastics which makes comparisons to other methods difficult as the conversion between number of MP particles to MP mass requires assumptions about size ranges and densities. Better knowledge of the size and densities of MPs is important for better comparison between methods and understanding their human health effects as smaller, less dense MPs reach deeper into the lungs.18 Pyr-GC/MS has limited repeatability as it is a destructive method. It also requires thorough organic removal and careful selection of pyrolysis products as indicators as common pyrolysis products like benzene and styrene are also produced by organic materials.67 However, the use of more specific indicators and calibrations based on standards limits false positives resulting from contamination and non-plastic organics that remain in the sample.57
Limits of detection differ between polymer types but are usually in the microgram scale.57 Shape, size, colour and additives do not affect the results as the decomposition products are the component being analysed and the additives decomposition can be determined simultaneously, which is another benefit of this method.36 Additionally, Pyr-GC/MS allows for the analysis of tyre wear particles which are challenging to analyse with spectroscopic methods like FTIR due to light absorption in the infrared region.84
Quality control and assurance
A range of measures are required to avoid contamination of samples during collection, preparation and analysis. For example, designs for the samplers should minimise plastic use and samplers should always be approached from down-wind. Cotton lab coats and natural clothing (i.e. cotton or wool) should always be used to limit the contamination from the user. The use of nitrile gloves washed with Milli-Q can minimise the potential transfer of fibres from fingertips to the sample.85
All equipment and work environments should be thoroughly cleaned. Many studies have used three successive rinsing steps and heated glassware where possible.85 Due to the ubiquitous nature of MPs, contamination cannot be prevented entirely and it is therefore critical to include field blanks and procedural blanks.85 The field blanks measure potential contamination during the sampling period, while the procedural blanks measure contamination throughout lab procedures such as filtration and sample handling.86 Positive controls, where a known number of MPs are processed and analysed, provide recoveries and an understanding of over or underestimation. As visual methods are prone to errors, a polymer specific analysis technique should always be used in combination.50,68
Conclusions
The field of airborne MPs is a fast-developing area of research with a variety of methods for detecting MPs being used. There are a range of considerations within quality control, filter types, sample preparation and analysis method which have not been standardised. Comparison between studies is difficult due to this lack of standardisation, which limits the understanding of the climate and health effects of airborne MPs. Developments must be made towards understanding the effects of sampler designs and resuspension of airborne MPs. Further work is needed on the best sample preparation process for airborne microplastics, which can remove organic debris whilst not impacting polymer types of interest. There is a need for the development of standardised methods for analysis in this field to ensure results globally can be compared and used to develop our understanding of airborne microplastics.
References
- Thompson, R. C.; Swan, S. H.; Moore, C. J.; vom Saal, F. S. Philos. Trans. R. Soc. Lond. B Biol. Sci. 2009, 364 (1526), 1973-1976. DOI: 10.1098/rstb.2009.0054.
- Baekeland, L. H. JIEC 1909, 1 (3), 149-161. DOI: 10.1021/ie50003a004.
- PlasticsEurope, E. Plastics—the facts 2019. An analysis of European plastics production, demand and waste data. PlasticEurope 2019.
- Lebreton, L.; Andrady, A. Palgrave Commun. 2019, 5 (1), 6. DOI: 10.1057/s41599-018-0212-7.
- Allen, D.; Allen, S.; Abbasi, S.; Baker, A.; Bergmann, M.; Brahney, J.; Butler, T.; Duce, R. A.; Eckhardt, S.; Evangeliou, N.; Jickells, T.; Kanakidou, M.; Kershaw, P.; Laj, P.; Levermore, J.; Li, D.; Liss, P.; Liu, K.; Mahowald, N.; Masque, P.; Materić, D.; Mayes, A. G.; McGinnity, P.; Osvath, I.; Prather, K. A.; Prospero, J. M.; Revell, L. E.; Sander, S. G.; Shim, W. J.; Slade, J.; Stein, A.; Tarasova, O.; Wright, S. Nat. Rev. Earth Environ. 2022, 3 (6), 393-405. DOI: 10.1038/s43017-022-00292-x.
- Aves, A. R.; Revell, L. E.; Gaw, S.; Ruffell, H.; Schuddeboom, A.; Wotherspoon, N. E.; LaRue, M.; McDonald, A. J. Cryosphere 2022, 16 (6), 2127-2145. DOI: 10.5194/tc-16-2127-2022.
- Bergmann, M.; Mützel, S.; Primpke, S.; Tekman, M. B.; Trachsel, J.; Gerdts, G. Sci. Adv. 2019, 5 (8), eaax1157. DOI: doi:10.1126/sciadv.aax1157.
- Joint Group of Experts on the Scientific Aspects of Marine Environmental Protection; Peter, J. K. Sources, fate and effects of microplastics in the marine environment: a global assessment; United Nations Educational, Scientific and Cultural Organisation 2015. https://policycommons.net/artifacts/8240132/sources-fate-and-effects-of-microplastics-in-the-marine-environment/.
- Sangkham, S.; Faikhaw, O.; Munkong, N.; Sakunkoo, P.; Arunlertaree, C.; Chavali, M.; Mousazadeh, M.; Tiwari, A. Mar. Pollut. Bull. 2022, 181, 113832. DOI: 10.1016/j.marpolbul.2022.113832.
- Cai, L.; Wang, J.; Peng, J.; Wu, Z.; Tan, X. Sci. Total Environ. 2018, 628-629, 740-747. DOI: 10.1016/j.scitotenv.2018.02.079.
- Jansen, M. A. K.; Andrady, A. L.; Bornman, J. F.; Aucamp, P. J.; Bais, A. F.; Banaszak, A. T.; Barnes, P. W.; Bernhard, G. H.; Bruckman, L. S.; Busquets, R.; Häder, D. P.; Hanson, M. L.; Heikkilä, A. M.; Hylander, S.; Lucas, R. M.; Mackenzie, R.; Madronich, S.; Neale, P. J.; Neale, R. E.; Olsen, C. M.; Ossola, R.; Pandey, K. K.; Petropavlovskikh, I.; Revell, L. E.; Robinson, S. A.; Robson, T. M.; Rose, K. C.; Solomon, K. R.; Andersen, M. P. S.; Sulzberger, B.; Wallington, T. J.; Wang, Q. W.; Wängberg, S.; White, C. C.; Young, A. R.; Zepp, R. G.; Zhu, L. Photochem. Photobiol. Sci. 2024. DOI: 10.1007/s43630-024-00552-3 From NLM.
- Rambacher, J.; Pantos, O.; Hardwick, S.; Cameron, E. Z.; Gaw, S. Transforming encounters: A review of the drivers and mechanisms of macrofaunal plastic fragmentation in the environment. Camb. prism., Plast. 2023, 1, e6. DOI: 10.1017/plc.2023.6 From Cambridge University Press Cambridge Core.
- Pironti, C.; Ricciardi, M.; Motta, O.; Miele, Y.; Proto, A.; Montano, L. Toxics 2021, 9 (9), 224. DOI: 10.3390%2Ftoxics9090224.
- Szewc, K.; Graca, B.; Dołęga, A. Sci. Total Environ. 2021, 761, 143272. DOI: 10.1016/j.scitotenv.2020.143272.
- Costa, J. P. d.; Avellan, A.; Mouneyrac, C.; Duarte, A.; Rocha-Santos, T. TrAC, Trends Anal. Chem. 2023, 158, 116898. DOI: 10.1016/j.trac.2022.116898.
- Wang, J.; Tan, Z.; Peng, J.; Qiu, Q.; Li, M. Mar. Environ. Res. 2016, 113, 7-17. DOI: 10.1016/j.marenvres.2015.10.014.
- Mato, Y.; Isobe, T.; Takada, H.; Kanehiro, H.; Ohtake, C.; Kaminuma, T. P. Environ. Sci. Technol. 2001, 35 (2), 318-324. DOI: 10.1021/es0010498.
- Prata, J. C.; da Costa, J. P.; Lopes, I.; Duarte, A. C.; Rocha-Santos, T. Sci. Total Environ. 2020, 702, 134455. DOI: 10.1016/j.scitotenv.2019.134455.
- Marfella, R.; Prattichizzo, F.; Sardu, C.; Fulgenzi, G.; Graciotti, L.; Spadoni, T.; D’Onofrio, N.; Scisciola, L.; La Grotta, R.; Frigé, C.; Pellegrini, V.; Municinò, M.; Siniscalchi, M.; Spinetti, F.; Vigliotti, G.; Vecchione, C.; Carrizzo, A.; Accarino, G.; Squillante, A.; Spaziano, G.; Mirra, D.; Esposito, R.; Altieri, S.; Falco, G.; Fenti, A.; Galoppo, S.; Canzano, S.; Sasso, F. C.; Matacchione, G.; Olivieri, F.; Ferraraccio, F.; Panarese, I.; Paolisso, P.; Barbato, E.; Lubritto, C.; Balestrieri, M. L.; Mauro, C.; Caballero, A. E.; Rajagopalan, S.; Ceriello, A.; D’Agostino, B.; Iovino, P.; Paolisso, G. N. Engl. J. Med. 2024, 390 (10), 900-910. DOI: 10.1056/NEJMoa2309822.
- Demirelli, E.; Tepe, Y.; Oğuz, U.; Aydın, H.; Kodat, M.; Tok, D. S.; Sönmez, M. G.; Öğreden, E. BMC Urol. 2024, 24 (1), 106. DOI: 10.1186/s12894-024-01495-8.
- Zhao, Q.; Zhu, L.; Weng, J.; Jin, Z.; Cao, Y.; Jiang, H.; Zhang, Z. Sci. Total Environ. 2023, 877, 162713. DOI: 10.1016/j.scitotenv.2023.162713.
- Revell, L. E.; Kuma, P.; Le Ru, E. C.; Somerville, W. R. C.; Gaw, S. Nature 2021, 598 (7881), 462-467. DOI: 10.1038/s41586-021-03864-x.
- Ganguly, M.; Ariya, P. A. ACS Earth Space Chem. 2019, 3 (9), 1729-1739. DOI: 10.1021/acsearthspacechem.9b00132.
- Aeschlimann, M.; Li, G.; Kanji, Z. A.; Mitrano, D. M. Nat. Geosci. 2022, 15 (12), 967-975. DOI: 10.1038/s41561-022-01051-9.
- Dris, R.; Gasperi, J.; Rocher, V.; Saad, M.; Renault, N.; Tassin, B. Environ. Chem. 2015, 12 (5), 592-599. DOI: 10.1071/EN14167.
- Zhang, Y.; Kang, S.; Allen, S.; Allen, D.; Gao, T.; Sillanpää, M. Earth-Sci. Rev. 2020, 203, 103118. DOI: 10.1016/j.earscirev.2020.103118.
- López-Rosales, A.; Ferreiro, B.; Andrade, J.; Fernández-Amado, M.; González-Pleiter, M.; López-Mahía, P.; Rosal, R.; Muniategui-Lorenzo, S. Sci. Total Environ. 2024, 913, 169678. DOI: 10.1016/j.scitotenv.2023.169678.
- Chenappan, N. K.; Ibrahim, Y. S.; Anuar, S. T.; Yusof, K. M. K. K.; Jaafar, M.; Ahamad, F.; Sulaiman, W. Z. W.; Mohamad, N. Environ. Monit. Assess. 2024, 196 (3), 242. DOI: 10.1007/s10661-024-12381-z.
- Xu, L.; Bai, X.; Li, K.; Zhang, G.; Zhang, M.; Hu, M.; Huang, Y. Environ. Sci. Technol. 2024, 58 (8), 3702-3713. DOI: 10.1021/acs.est.3c09271.
- Abbasi, S. J. Hazard. Mater. Adv. 2021, 4, 100035. DOI: 10.1016/j.hazadv.2021.100035.
- Allen, S.; Allen, D.; Phoenix, V. R.; Le Roux, G.; Durántez Jiménez, P.; Simonneau, A.; Binet, S.; Galop, D. Nat. Geosci. 2019, 12 (5), 339-344. DOI: 10.1038/s41561-019-0335-5.
- Brahney, J.; Hallerud, M.; Heim, E.; Hahnenberger, M.; Sukumaran, S. Science 2020, 368 (6496), 1257-1260. DOI: doi:10.1126/science.aaz5819.
- Knobloch, E.; Ruffell, H.; Aves, A.; Pantos, O.; Gaw, S.; Revell, L. E. Water, Air, Soil Pollut. 2021, 232 (4), 133. DOI: 10.1007/s11270-021-05080-9.
- Aves, A.; Ruffell, H.; Evangeliou, N.; Gaw, S.; Revell, L. E. Atmos. Environ. 2024, 120437. DOI: 10.1016/j.atmosenv.2024.120437.
- Levermore, J. M.; Smith, T. E. L.; Kelly, F. J.; Wright, S. L. Anal. Chem. 2020, 92 (13), 8732-8740. DOI: 10.1021/acs.analchem.9b05445.
- Chen, G.; Fu, Z.; Yang, H.; Wang, J. TrAC, Trends Anal. Chem. 2020, 130, 115981. DOI: 10.1016/j.trac.2020.115981.
- Huang, Y.; Qing, X.; Wang, W.; Han, G.; Wang, J. TrAC, Trends Anal. Chem. 2020, 125, 115821. DOI: 10.1016/j.trac.2020.115821.
- Shao, L.; Li, Y.; Jones, T.; Santosh, M.; Liu, P.; Zhang, M.; Xu, L.; Li, W.; Lu, J.; Yang, C.-X.; Zhang, D.; Feng, X.; BéruBé, K. J. Clean. Prod. 2022, 347, 131048. DOI: 10.1016/j.jclepro.2022.131048.
- Rani, M.; Ducoli, S.; Depero, L. E.; Prica, M.; Tubić, A.; Ademovic, Z.; Morrison, L.; Federici, S. Molecules 2023, 28 (15). DOI: 10.3390/molecules28155710 From NLM.
- Erni-Cassola, G.; Gibson, M. I.; Thompson, R. C.; Christie-Oleza, J. A. Environ. Sci. Technol. 2017, 51 (23), 13641-13648. DOI: 10.1021/acs.est.7b04512.
- Shruti, V. C.; Pérez-Guevara, F.; Roy, P. D.; Kutralam-Muniasamy, G. J. Hazard. Mater. 2022, 423, 127171. DOI: 10.1016/j.jhazmat.2021.127171.
- Pico, Y.; Alfarhan, A.; Barcelo, D. TrAC, Trends Anal. Chem. 2019, 113, 409-425. DOI: 10.1016/j.trac.2018.08.022.
- Cai, L.; Wang, J.; Peng, J.; Tan, Z.; Zhan, Z.; Tan, X.; Chen, Q. Environ. Sci. Pollut. Res. 2017, 24 (32), 24928-24935. DOI: 10.1007/s11356-017-0116-x.
- Pfeiffer, F.; Fischer, E. K. Front. Environ. Sci. 2020, 8. DOI: 10.3389/fenvs.2020.572424.
- Schrank, I.; Möller, J. N.; Imhof, H. K.; Hauenstein, O.; Zielke, F.; Agarwal, S.; Löder, M. G. J.; Greiner, A.; Laforsch, C. Sci. Total Environ. 2022, 833, 154824. DOI: 10.1016/j.scitotenv.2022.154824.
- Pfohl, P.; Roth, C.; Meyer, L.; Heinemeyer, U.; Gruendling, T.; Lang, C.; Nestle, N.; Hofmann, T.; Wohlleben, W.; Jessl, S. Microplast. Nanoplast. 2021, 1 (1), 8. DOI: 10.1186/s43591-021-00009-9.
- Al-Azzawi, M. S. M.; Kunaschk, M.; Mraz, K.; Freier, K. P.; Knoop, O.; Drewes, J. E. Sci. Total Environ. 2023, 863, 160947. DOI: 10.1016/j.scitotenv.2022.160947.
- Charbonnet, J. A.; McDonough, C. A.; Xiao, F.; Schwichtenberg, T.; Cao, D.; Kaserzon, S.; Thomas, K. V.; Dewapriya, P.; Place, B. J.; Schymanski, E. L.; Field, J. A.; Helbling, D. E.; Higgins, C. P. Environ. Sci. Technol. Lett. 2022, 9 (6), 473-481. DOI: 10.1021/acs.estlett.2c00206 From NLM.
- Löder, M. G. J.; Gerdts, G. Methodology Used for the Detection and Identification of Microplastics—A Critical Appraisal. In Marine Anthropogenic Litter; Bergmann, M., Gutow, L., Klages, M., Eds.; Springer International Publishing: Cham, 2015; pp 201-227.
- Hidalgo-Ruz, V.; Gutow, L.; Thompson, R. C.; Thiel, M. Environ. Sci. Technol. 2012, 46 (6), 3060-3075. DOI: 10.1021/es2031505.
- Chandrakanthan, K.; Fraser, M. P.; Herckes, P. Atmos. Environ. 2023, 298, 119617. DOI: 10.1016/j.atmosenv.2023.119617.
- Ferreiro, B.; Andrade, J. M.; Paz-Quintáns, C.; Fernández-González, V.; López-Mahía, P.; Muniategui, S. Mar. Pollut. Bull. 2022, 181, 113897. DOI: 10.1016/j.marpolbul.2022.113897.
- Song, Y. K.; Hong, S. H.; Jang, M.; Han, G. M.; Rani, M.; Lee, J.; Shim, W. J. Mar. Pollut. Bull. 2015, 93 (1), 202-209. DOI: 10.1016/j.marpolbul.2015.01.015.
- Xu, J.-L.; Thomas, K. V.; Luo, Z.; Gowen, A. A. TrAC, Trends Anal. Chem. 2019, 119, 115629. DOI: 10.1016/j.trac.2019.115629.
- Whiting, Q. T.; O’Connor, K. F.; Potter, P. M.; Al-Abed, S. R. Anal. Bioanal. Chem. 2022, 414 (29), 8353-8364. DOI: 10.1007/s00216-022-04371-2.
- Höppener, E. M.; Shahmohammadi, M.; Parker, L. A.; Henke, S.; Urbanus, J. H. Talanta 2023, 253, 123985. DOI: 10.1016/j.talanta.2022.123985.
- Santos, L. H. M. L. M.; Insa, S.; Arxé, M.; Buttiglieri, G.; Rodríguez-Mozaz, S.; Barceló, D. MethodsX 2023, 10, 102143. DOI: 10.1016/j.mex.2023.102143.
- Leusch, F. D. L.; Lu, H.-C.; Perera, K.; Neale, P. A.; Ziajahromi, S. Environ. Pollut. 2023, 319, 120984. DOI: 10.1016/j.envpol.2022.120984.
- Beckingham, B.; Apintiloaiei, A.; Moore, C.; Brandes, J. Microplast. Nanoplast. 2023, 3 (1), 8. DOI: 10.1186/s43591-023-00056-4.
- Li, J.; Liu, H.; Paul Chen, J. Water Res. 2018, 137, 362-374. DOI: 10.1016/j.watres.2017.12.056.
- Greenspan, P.; Mayer, E. P.; Fowler, S. D. J. Cell Biol. 1985, 100 (3), 965-973. DOI: 10.1083/jcb.100.3.965.
- Maes, T.; Jessop, R.; Wellner, N.; Haupt, K.; Mayes, A. G. Sci. Rep. 2017, 7 (1), 44501. DOI: 10.1038/srep44501.
- Klein, M.; Fischer, E. K. Sci. Total Environ. 2019, 685, 96-103. DOI: 10.1016/j.scitotenv.2019.05.405.
- Mason, S. A.; Welch, V. G.; Neratko, J. Frontiers in Chemistry 2018, 6. DOI: 10.3389/fchem.2018.00407.
- Kankanige, D.; Babel, S. J. Water Process Eng. 2021, 40, 101765. DOI: 10.1016/j.jwpe.2020.101765.
- Ranjan, V. P.; Joseph, A.; Goel, S. J. Hazard. Mater. 2021, 404, 124118. DOI: 10.1016/j.jhazmat.2020.124118.
- Fan, W.; Salmond, J. A.; Dirks, K. N.; Cabedo Sanz, P.; Miskelly, G. M.; Rindelaub, J. D. Environ. Sci. Technol. 2022, 56 (24), 17556-17568. DOI: 10.1021/acs.est.2c05850.
- Wiggin, K. J.; Holland, E. B. Mar. Pollut. Bull. 2019, 143, 152-162. DOI: 10.1016/j.marpolbul.2019.03.060.
- Tamminga, M.; Stoewer, S.-C.; Fischer, E. K. Environ. Pollut. 2019, 254, 112970. DOI: 10.1016/j.envpol.2019.112970.
- Käppler, A.; Fischer, D.; Oberbeckmann, S.; Schernewski, G.; Labrenz, M.; Eichhorn, K.-J.; Voit, B. Anal. Bioanal. Chem. 2016, 408 (29), 8377-8391. DOI: 10.1007/s00216-016-9956-3.
- Tisch Scientific. Whatman Anodisc Anapore Inorganic Membranes. https://scientificfilters.com/whatman/membranes/inorganic-membranes (accessed 21/11/2024).
- Gillibert, R.; Balakrishnan, G.; Deshoules, Q.; Tardivel, M.; Magazzù, A.; Donato, M. G.; Maragò, O. M.; Lamy de La Chapelle, M.; Colas, F.; Lagarde, F.; Gucciardi, P. G. Environ. Sci. Technol. 2019, 53 (15), 9003-9013. DOI: 10.1021/acs.est.9b03105.
- Cheng, Y.-L.; Zhang, R.; Tisinger, L.; Cali, S.; Yu, Z.; Chen, H. Y.; Li, A. Gondwana Res. 2022, 108, 22-30. DOI: 10.1016/j.gr.2021.10.002.
- Lavoie-Bernstein, S. Comparing Sampling Methods for Measuring Atmospheric Microplastics in Rural and Urban Sites, using Laser Direct Infrared Spectroscopy (LDIR). Master’s Thesis, University of Toronto, 2024. https://hdl.handle.net/1807/138047.
- Ourgaud, M.; Phuong, N. N.; Papillon, L.; Panagiotopoulos, C.; Galgani, F.; Schmidt, N.; Fauvelle, V.; Brach-Papa, C.; Sempéré, R. Environ. Sci. Technol. 2022, 56 (14), 9999-10009. DOI: 10.1021/acs.est.1c08870.
- Borman, S. A. Anal. Chem. 1982, 54 (9), 1021A-1026A. DOI: 10.1021/ac00246a002.
- Araujo, C. F.; Nolasco, M. M.; Ribeiro, A. M. P.; Ribeiro-Claro, P. J. A. Water Res. 2018, 142, 426-440. DOI: 10.1016/j.watres.2018.05.060.
- Primpke, S.; Christiansen, S. H.; Cowger, W.; De Frond, H.; Deshpande, A.; Fischer, M.; Holland, E. B.; Meyns, M.; O'Donnell, B. A.; Ossmann, B. E.; Pittroff, M.; Sarau, G.; Scholz-Böttcher, B. M.; Wiggin, K. J. Appl. Spectrosc. 2020, 74 (9), 1012-1047. DOI: 10.1177/0003702820921465.
- Chou, S.-H.; Chuang, Y.-K.; Lee, C.-M.; Chang, Y.-S.; Jhang, Y.-J.; Yeh, C.-W.; Wu, T.-S.; Chuang, C.-Y.; Hsiao, I. L. Environ. Pollut. 2022, 300, 118964. DOI: 10.1016/j.envpol.2022.118964.
- Kung, H.-C.; Wu, C.-H.; Cheruiyot, N. K.; Mutuku, J. K.; Huang, B.-W.; Chang-Chien, G.-P. Aerosol Air Qual. Res. 2023, 23 (1), 220362. DOI: 10.4209/aaqr.220362.
- Wagner, J.; Wang, Z.-M.; Ghosal, S.; Rochman, C.; Gassel, M.; Wall, S. Anal. Methods [10.1039/C6AY02396G] 2017, 9 (9), 1479-1490. DOI: 10.1039/C6AY02396G.
- Wang, Z.-M.; Wagner, J.; Ghosal, S.; Bedi, G.; Wall, S. Sci. Total Environ. 2017, 603-604, 616-626. DOI: 10.1016/j.scitotenv.2017.06.047.
- Torres-Agullo, A.; Zuri, G.; Lacorte, S. J. Hazard. Mater. 2024, 469, 133981. DOI: 10.1016/j.jhazmat.2024.133981.
- Rosso, B.; Gregoris, E.; Litti, L.; Zorzi, F.; Fiorini, M.; Bravo, B.; Barbante, C.; Gambaro, A.; Corami, F. Environ. Pollut. 2023, 326, 121511. DOI: 10.1016/j.envpol.2023.121511.
- Dehaut, A.; Hermabessiere, L.; Duflos, G. TrAC, Trends Anal. Chem. 2019, 116, 346-359. DOI: 10.1016/j.trac.2018.11.011.
- Noonan, M. J.; Grechi, N.; Mills, C. L.; de A. M. M. Ferraz, M. Microplast. Nanoplast. 2023, 3 (1), 17. DOI: 10.1186/s43591-023-00065-3.